Case Study: 3PL Experiences Dramatic Improvements via Custom Protective Packaging | Pregis
3PL experiences dramatic improvements to operation, reduction in damage rates via custom protective packaging solutions from Pregis
Third-party logistics companies, commonly known as 3PLs, provide a variety of services, including fulfillment for a diverse range of customers and products. This means that the protective packaging solutions available at each fulfillment operation need to accommodate those wide-ranging needs. One national, e-commerce fulfillment 3PL company, with multiple locations across the United States, was faced with exactly that dilemma as its business began to grow rapidly during the COVID-19 pandemic
Problem
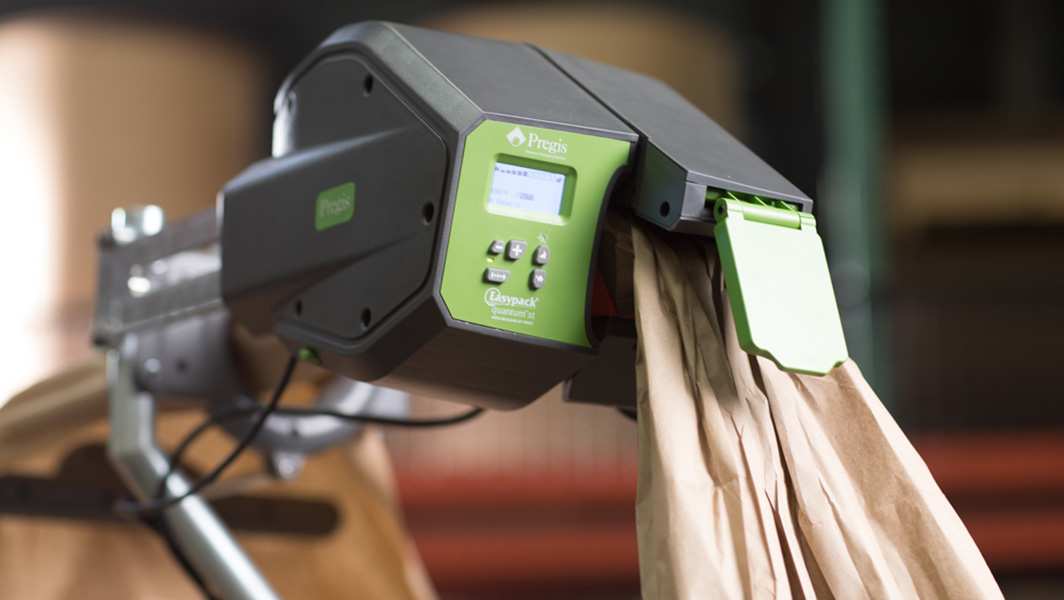
Easypack® Quantum™ XT paper void-fill system
A few years back when the 3PL was first scaling, it asked Pregis to provide a quote for its Easypack® Quantum™ XT paper void-fill system, which had been engineered for high-volume operations. However, the 3PL ended up going with a lower-cost system from a different company. The negative impact from this decision was significant.
For example, the original system was used to create paper void-fill for a security camera product. Unfortunately, the void-fill did not properly protect the product, resulting in 3.8% of the shipments being damaged in transit. Security cameras are typically priced between $100 to $300. Damage to these sensitive electronics not only impact both the brand owner and 3PL financially, but since they frequently cannot be repaired, they have to be scrapped and end up in a landfill, seriously impacting the environment.
The original paper system also caused significant downtime when packaging an upscale, online eyeglass line. Extensive machine jamming caused 10% downtime per day, resulting in a productivity decline of 15% over a period of 10 months. Further, employees had to be diverted from other functions to address the equipment malfunction.
Multiple customers were upset and the unnecessary expense of damages, downtime, and labor continued to grow.
Solution
Pregis was brought back in by the 3PL to address the issue. However, this time, Pregis was allowed to do an audit of the various products and what protective packaging approach(es) would best suit the 3PL. Since each fulfillment center is responsible for packaging 100 or more products, one packaging solution would not work for all. Pregis, not only had to review the product types, but also consider the packing stations, floor space, packaging material inventory, target throughput, labor, ergonomics and, of course, economics. If the solution cost more, there would have to be significant benefits to justify the additional expenditure.
The first part of the solution was to convert the operation to Easypack® Quantum™ XT on-demand systems for those products where paper void-fill was the ideal solution. The feature-rich machine offers high productivity, ease-of-use,safety, superior ergonomics, paper-loading ease, as well as, flexible design which enables customized work cell options. The packing material recommendation for the 3PL was 15-inch wide, Forest Stewardship Council® (FSC)-certified, fan-fold, 30-pound paper.
The second recommendation was to bring in a hybrid cushioning (HC) solution produced on Pregis’ AirSpeed® HC Versa on-demand machine for more sensitive products like the security cameras mentioned previously. Hybrid cushioning differs from traditional void-fill pillows because it features multiple air chambers in a horizontal and vertical pattern vs. one large cell. Flat, perforated roll stock is mounted onto the AirSpeed unit, which creates the rows of small air-filled pockets as the air is transferred between the individual chambers. The proprietary pattern enables superior air retention which improves product protection.
The third recommendation was to automate bagging operations via the company’s Sharp® SX GO, compact, tabletop bagging system that can fit bags up to 18"-wide. This easy-to-use bagging system can label, address, open, fill and bags. The unit can be mounted onto existing workstations or other compact areas not suited to a floor model design.
All three options were tested using actual products at the Pregis Innovation Headquarters (customer-focused training, design and testing services hub) to ensure that performance parameters were met. A fourth option, Pregis Eco Mailer, lightweight, curbside recyclable all-paper mailer, was also offered to help address sustainability issues.
Outcome
During the initial 30 days after installation, Pregis technicians were on location at the various fulfillment centers to make sure that the onboarding of all equipment types was seamless. Once the new systems were up and running, the 3PL was able to realize the following benefits.
Productivity savings. The competitive machines that Pregis replaced were hard to load and struggled with jamming issues. By switching to the Quantum units, the 3PL has experienced an increase in productivity of 12 hours per week, which equates to approximately $45,000 per year.
By adding Sharp baggers to the outbound lines, the 3PL realized a productivity increase of approximately 350%. Packing improved from 2 to 7 packs per minute, which has helped the 3PL keep up with higher demand as well as reduce labor. The total savings associated with this change is approximately $75,000 per year.
Space savings. By attaching the Quantum void-fill paper units to pack stations, 9 sq. ft. of space at each pack station was freed up and converted into much needed box storage.
Material savings. Switching from a #40 paper to Pregis’ #30 paper, the 3PL was able to reduce costs by $60,000 per year without sacrificing quality or protection.
Damage reduction. By incorporating the HC product into its operation, damages were reduced by 5% (approximately $120,000 annually) on their breakable items, resulting in a current damage rate of 0.4%.
Increased safety. The 3PL viewed the blades on the original paper machine as a potential safety hazard. The bladeless cutting mechanism on the Quantum machine was a welcome addition to its fulfillment centers.